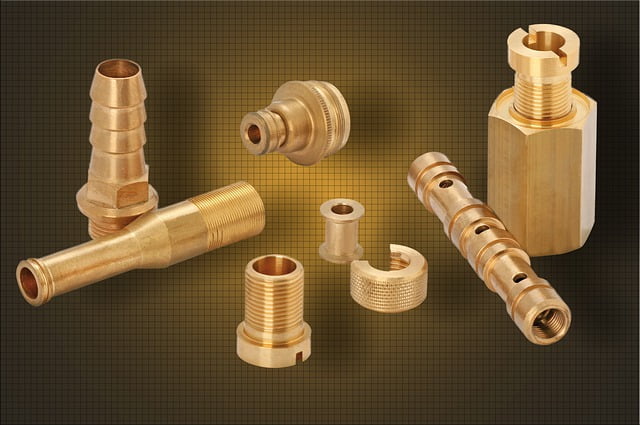
It costs you time, money and material to run customer service. Spare parts usage is among the first things you need to track.
Spare parts are expensive – tracking wrong use or misuse can save you money.
Read more on how to save money using intelligent spares parts management
You need to ensure:
- The right spare parts are used for the right equipment
- The right amount of consumables are used
- Spare parts availability with the engineers
- Stock audit compliance
Spare parts management helps select right parts for the right equipment
In case of spare parts usage, we do not want the decision to be left to the technician on the spot.
As with repair, we want him to “follow the manual”.
We want him to follow the prescribed procedure. And, also to use the right parts. Because, if he did not, there could be bad consequences from machine health perspective.
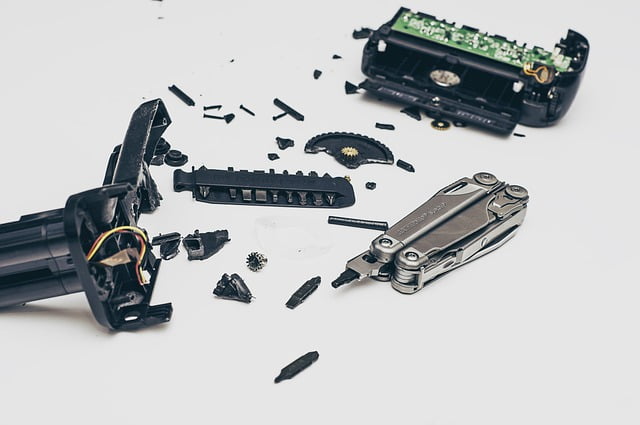
The simplest example is when you replace a “fuse” wire. The temptation to go over and under specification is huge- especially if you do not happen to have the right “fuse-wire” with you.
Of course this can lead to disaster.
Not all mis-use or wrong-use leads to disasters. But, should the technician decide? Let technology help him with suggesting spares that need to be used.
Spare parts management software- right amount of consumables
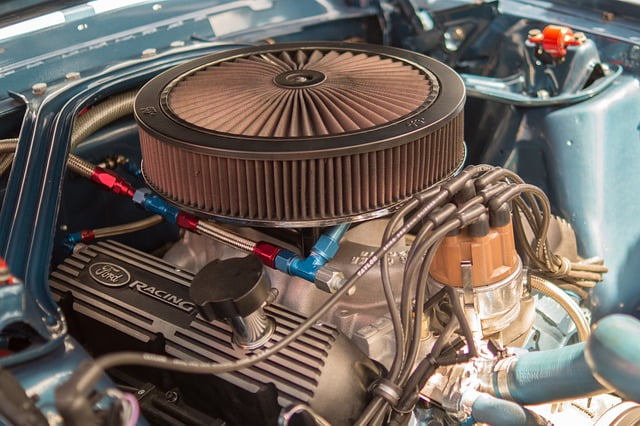
Let’s say your car goes for servicing- and the lube oil needs to be changed. Of course different cars need different amount of lubes. And the software guides the technician on how much is right.
And the same software helps, if you are managing a team of technicians, to ensure that the right amount of lube is used for the right car.
Consumables or spare parts usage, technology helps.
Plan right stocking levels for optimum spare parts usage
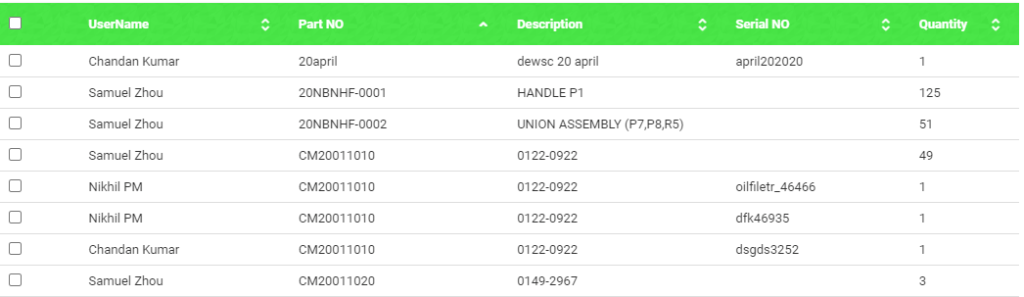
You need to plan for the right stocking levels of spare parts- at all levels.
Plan for urgent and frequently used spare parts usage and availability with your technicians.
Plan for re-stocking based on spare parts usage.
A spare parts management software integrated with your service CRM will help you plan against nasty surprises.
Comply with stock audit for parts
Stock audit is an integral part of spare parts management. It happens once a year but when it does, your numbers should match the physical audit.
Saleswah CRM helps.
Since no parts are used without being indented for and approved. Since we track parts usage at the lowest point from the central stocking point and every point in between. Since we can produce reports for stock levels availability.
Physical stock taking of spare parts usage is a breeze.